WLC qualities from the Gernsbach mill – perfect for blister applications
Blister packages are transparent packages that allow the manufacturer to package products in pre-fabricated, custom-fit moulds.
The product is presented in front of a cartonboard back that is usually printed with information, and held in place by a plastic foil mould, the actual blister. Even sensitive small parts are kept safe and protected from dislocation, abrasion, or breakage. The big advantage of this type of packaging is that the customer can see the product in its original appearance before buying it.
High demands on the cartonboard
Successful manufacturing of blister packages is a highly complex process and depends on a number of factors such as machining parameters, proper storage conditions or room climate, and particularly on the materials used. The list of demands placed on the cartonboard is long: high plybond strength of the cartonboard layers, perfect coating adherence on the raw cartonboard, good ink absorption properties, excellent varnishing properties of the coated surface, good printability of the reverse side, etc.
To seal the package, the blister is usually fused with the backing material by means of heat sealing. This is applied by activating the heat seal layer (blister coating) in the seams through pressure and heat. The thicker a blister carton, the longer the sealing time needs to be under consistent conditions. If it is not adapted to the specific heat permeation time of the cartonboard, the necessary softening temperature of the coating cannot be reached and a proper seal cannot be achieved. Once the package is properly sealed, it can only be opened by destroying it, so it offers sufficient theft protection for the goods inside. With a deficient seal, the blister can partially or entirely peel away from the cartonboard without fibre tear.
Top scores for Multicolor Mirabell™, Supra™ and Printa™
We have subjected our recycled cartonboard qualities to an extensive blister test (see information table on test set-up) and the result was very positive: all MMK WLC qualities showed perfect seals, and the GD2 qualities Multicolor Mirabell™ and Printa™ as well as the GT2 quality Supra™ from the German Gernsbach mill received top scores. All of them have broad, consistently strong fibre tear in the cartonboard after removal of the foil, which makes them ideal for blister packages.
Feel free to contact us if you are faced with a special challenge! Building on our decades of experience, we will work with you to develop the tailor-made blister packaging for your product.
MMK blister test – the test set-up
16 MMK cartonboard qualities were examined in the blister test. The following parameters were chosen:
Printing machine | KBA Rapida 105 Pro 6+L |
Printing ink | Process inks, low-migration, silver |
Blister coating | Actega G9/415 (standard coating) |
Anilox roller | Anilox roller Haschur 20 cm3 – ca. 8 gsm (standard) Anilox roller Haschur 17 cm3 – ca. 6 gsm (minimum) |
Blister foils | PET-G, PET-A, PVC |
Standard blister settings | 180 °C/5 bar/2 sec. |
During the function test of blister suitability, the 16 MMK cartonboard qualities were printed with identical 5-color print designs (4C+Silver). At consistent machine speed (12,000 sheets/hour) and dryer setting (32 °C), a defined amount of each cartonboard was processed with a coating of 8 gsm (standard) and alternatively with a coating of 6 gsm (minimum). Subsequently, blister cards were made from all materials, which were fused with PET-G, PET-A, and PVC foils at the recommended standard settings (temperature 180 °C, fusion pressure 5 bar, fusion time 2 sec.) on a heat sealing machine by Brugger Feinmechanik GmbH.
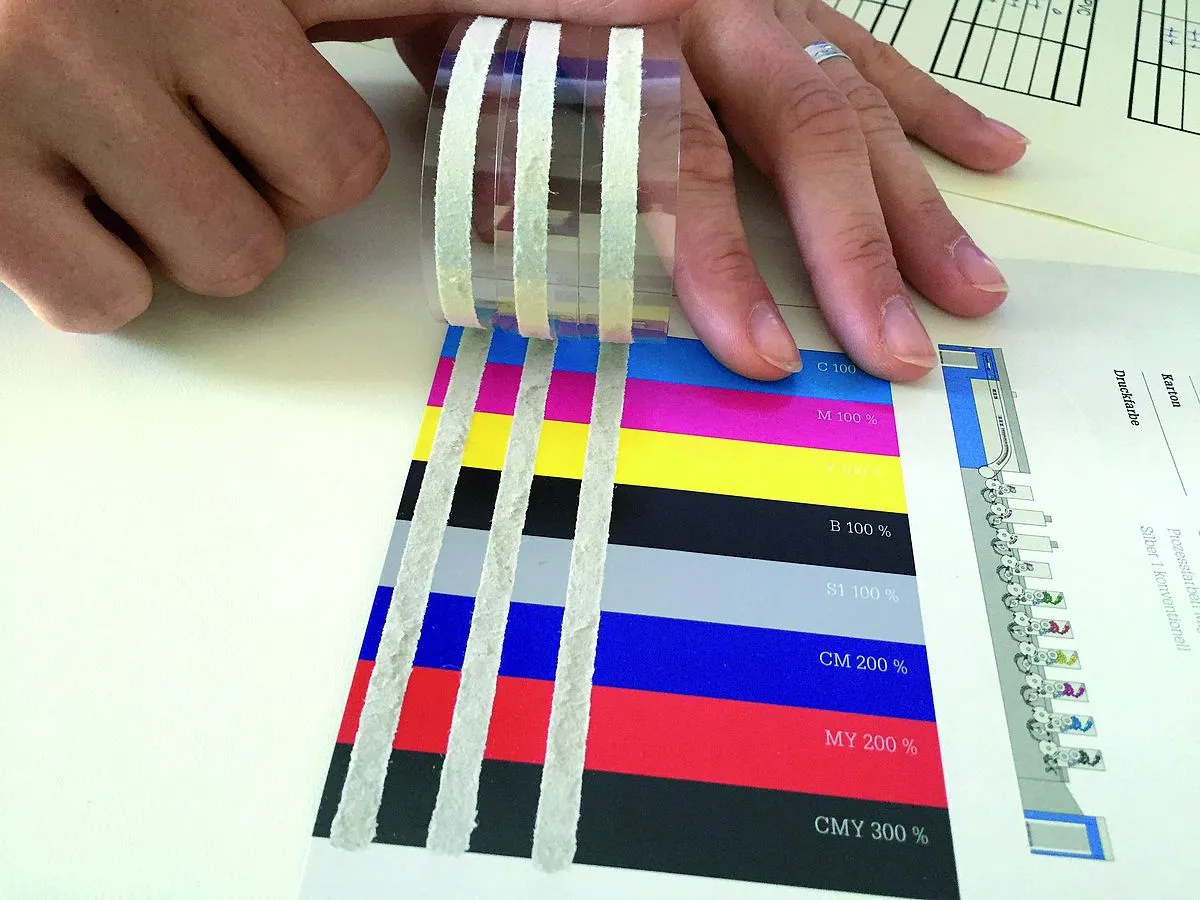
A very good seal was achieved even with the minimal coating amount, however, the standard amount is recommended for consistent process reliability.