Partnering for success: Technical product service that strengthens your packaging process
When the packaging line stops, everything stops. Delivery deadlines are missed, costs surge, and customer trust is at risk. These are the challenges that MM Board & Paper’s Technical Product Service team (TPS) works proactively to prevent. By supporting customers with technical know-how and expertise, the TPS team ensures that board grades perform reliably.
This service approach was recently put into action at MM Premium Vienna, where two of the company’s board grades, ALASKA® STRONG and ALASKA® SMART, were tested on packaging lines dedicated to a major brand. Both products are known for their strength, efficiency, and consistency, but integrating new materials into complex converting processes is never without a risk.
Proven performance under real production conditions
During the MM Premium Vienna assignment, the TPS team sought to verify that key operational requirements were met, with a focus on reliability, material handling and consistent product quality. Collaborating closely with the local production team, Gamba examined each stage of the converting workflow, fine-tuned machine settings, and pinpointed specific areas for improvement. This hands-on approach enabled swift adaptations, ensuring both board grades performed effectively under real-world conditions.
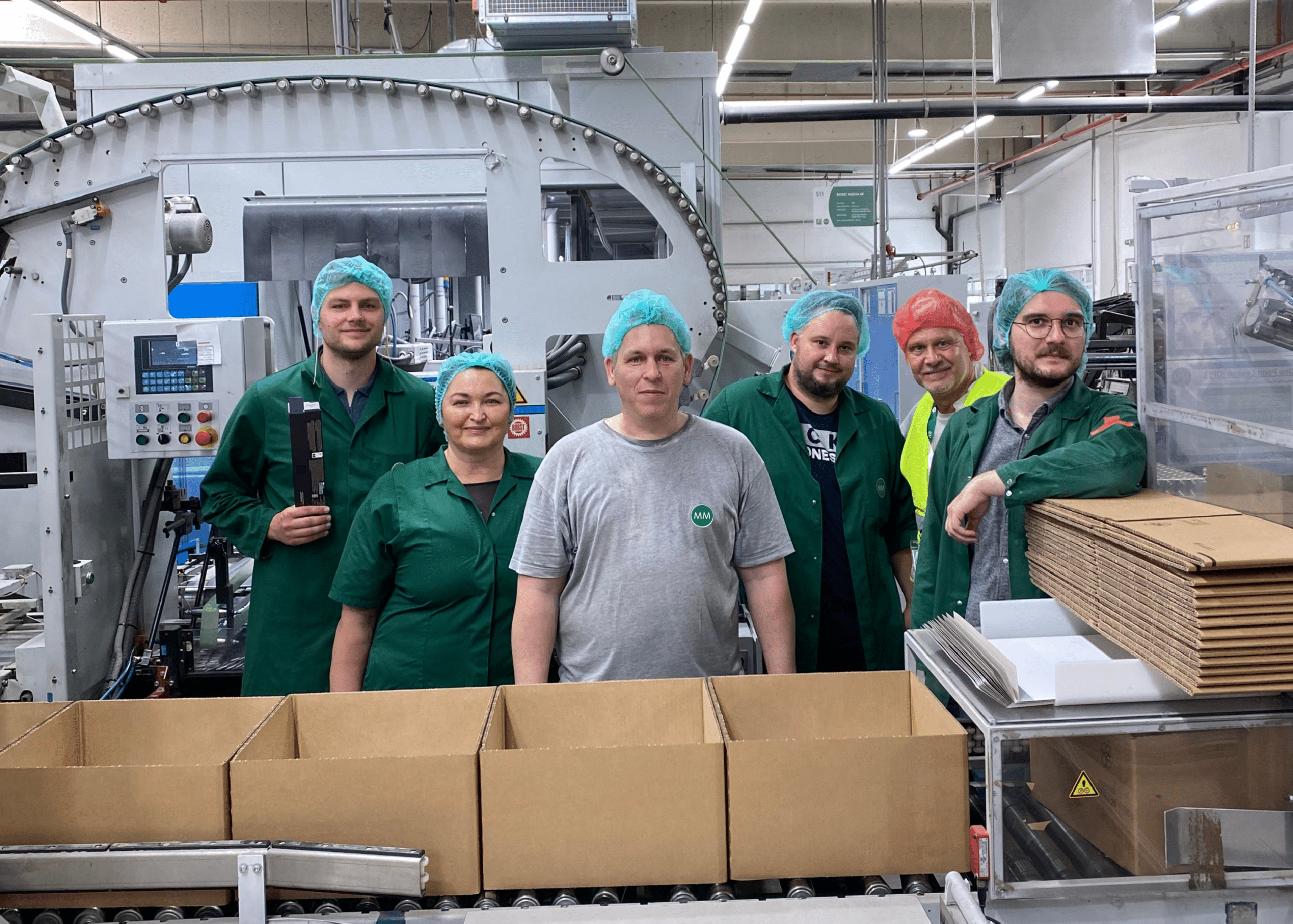
The same methodology was applied at MM Neupack where the TPS team tested ALASKA® STRONG and ALASKA® SMART – this time for packaging used in the premium beverage segment. Despite different equipment and local production conditions, both board grades demonstrated reliable and consistent results.
This consistency across sites underlines the versatility of MM Board & Paper’s portfolio and the TPS team’s ability to realize a material’s potential in production reality.
A service tailored to customer needs
TPS assignments are a fundamental aspect of how MM engages with its customers. Having technical experts on site enables rapid adjustments, process optimisation, and immediate troubleshooting. This minimizes the risk of production delays and helps maintain high-quality standards.
For businesses aiming to improve operational support, TPS offers a clear advantage: fewer interruptions, faster ramp-up, and greater process stability. In demanding production environments, the TPS team’s reliability brings measurable value in terms of production costs and brand reputation.