Friessinger Mühle protects its products with FOODBOARD™
Frießinger Mühle, one of Germany’s leading industrial mills, has decided to switch to FOODBOARD™ in the interest of highest product safety. The decision demonstrates the company’s commitment to responsible safety management along the entire supply chain.
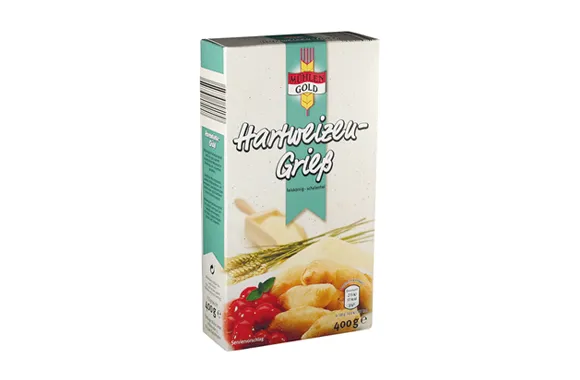
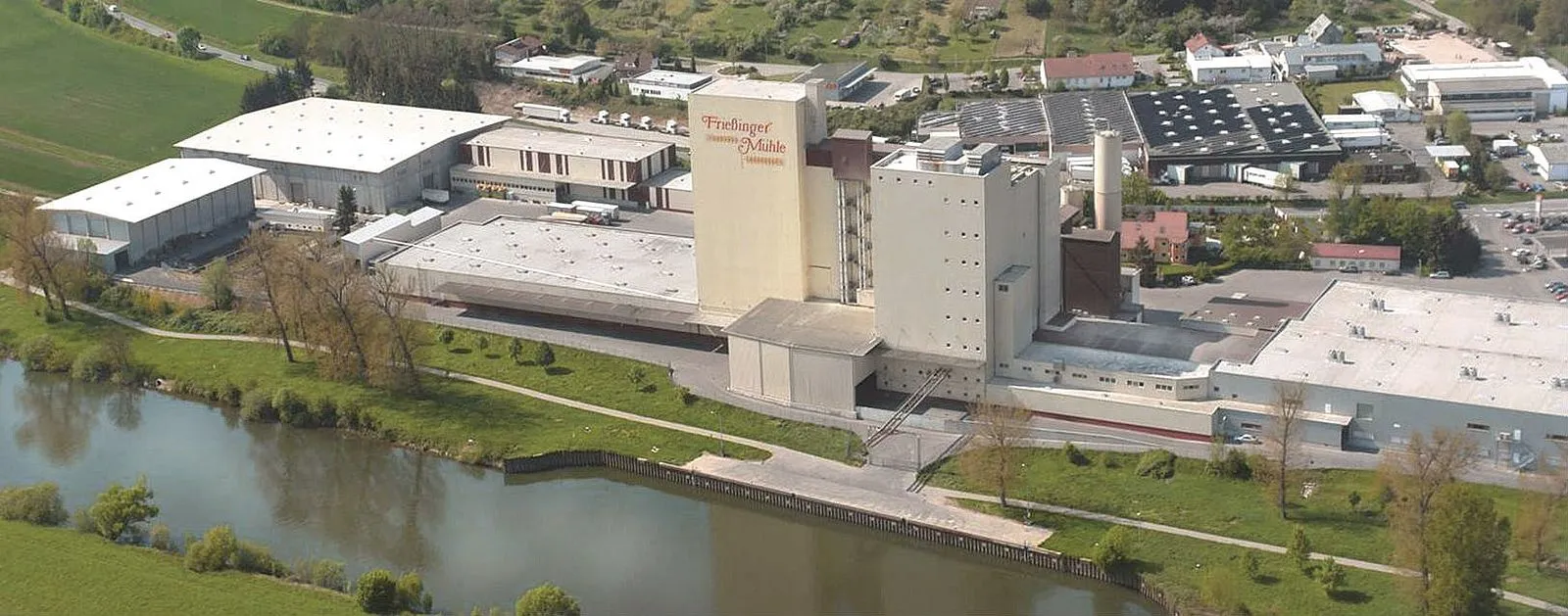
Since the beginning of 2017, packaging for products like durum wheat semolina and sauce thickener are made from FOODBOARD™. Willi Erich Frießinger, Junior Manager of Frießinger Mühle, explains the company’s quality standards and the reasons for the switch:
1. How are “quality” and “product safety” practiced in your organisation?
We can guarantee the high quality and safety of our Frießinger Mühle products by conducting consistent quality checks during the entire production process (random sampling, analyses), as well as through certifications (e.g. IFS Food) with unannounced audits, and through corresponding employee training.
2. What aspects are most important to you regarding your selection of packaging material?
Crucial factors for choosing a packaging material are primarily the supplier’s reliability, quick availability and short delivery times of the packaging material, and its “runnability” on our production systems.Product safety is of course a basic prerequisite: The material has to comply with the standards of the fourth draft of the German Mineral Oil Regulation for MOAH.
3. The company Frießinger Mühle has dealt intensively with the topic of packaging safety. What was the main reason?
We wanted to be pro-active in anticipating German legislation. The topic is discussed in the media more and more, so customers who justifiably have high product safety standards inquire about it frequently.
4. What solutions were considered?
We inquired about alternatives from other cartonboard converters. However, no other supplier was able to guarantee the degree of product safety that FOODBOARD™ offers.
5. What are the evaluation processes for FOODBOARD™?
Our product packaging and processes were evaluated and adapted in close cooperation with Mayr-Melnhof Karton, and we conducted extensive tests. The process was complex, but it was the only way to ensure that no migration of mineral oils and other unintended substances occurs.
6. What was the reason for switching to FOODBOARD™?
One reason was that by switching to FOODBOARD™, we are taking on a pioneering role in the German mill industry and thus getting one step ahead of the competition with regard to product safety. There is hardly any price difference, since we previously used packaging made of virgin fibre which did not always protect the contents 100 % either. Now we can use a recycling material, which contributes to environmentally-friendly and resource-oriented production.
7. Was consistent traceability of the packaging throughout the entire production process an argument for switching?
Certainly the fact that the entire conversion process is documented and controlled was a contributing factor, and that the customer can trace the package by means of the EAN code.
8. Why did you switch to FOODBOARD™ already, even before the German legislation comes into effect?
Our customers’ requirements and requests are increasing, even without legislation. It is a very good selling point for us, and keeps us ahead in the market.
Frießinger Mühle GmbH
The Frießinger Mühle company has been family owned since its foundation by Johann Jakob Frießinger in 1859. While the grain used to be ground with wind and water power, the modern operation in Bad Wimpfen is a high-performing industrial mill. With its own shipping port on the Neckar River, it is connected worldwide via European waterways. In addition to high-quality milling products, the company offers a broad range of ingredients for anything from pasta production to convenience products for industry, bakeries, and private households. To guarantee the quality of its products, the mill uses only carefully selected raw materials. Frießinger Mühle believes in buying locally and covers 90 % of its requirement for quality wheat and spelt from farms in the surrounding area. The mill is certified for its energy management, the International Food Standard, feed and organic production, and kosher production, with a worldwide export portion of 25 %. The expansion opportunities available in Bad Wimpfen allow the mill to grow steadily. Currently, Frießinger Mühle has a staff of 220 employees and processes more than 800 tons of grain per day.
For further information, please contact our team of experts:
FOODBOARD@mm-karton.com
Interested? Datasheet and Samples of
FOODBOARD™ can be found here: